QUALITY ASSURANCE
Quality assurance (QA) is a defined procedure that identifies whether a product or a service meets the set standards. QA in the context of welding and fabrication is a system that guarantees that all the processes in the fabrication of the weldment meet the set quality standards of the industry and that of the client. This involves the development of a plan, documentation and periodic check to ensure that the plan has been implemented. QA is centered on avoiding defects and putting in place measures that guarantee the end product is free from flaws.
QUALITY CONTROL
Quality control (QC) is defined as the procedures and measures employed to perform quality requirements. This is the physical examination and evaluation of materials, parts, assemblies, and finished goods to check their conformity to the set requirements. In welding, QC is essential in detecting defects in welds, materials, and workmanship before they are incorporated into the final product. These are the visual inspection, dimensional measurements, and destructive and non-destructive tests to ensure the quality and safety of the welded structures.
What Can Happen if QA & QC Procedures are Not Followed?
A lack of QA and QC can result in various drawbacks, such as structural failures, safety risks, higher costs, and a company’s reputation loss. Low-quality welding can lead to the formation of leaks, cracks or even failure of structures like pipes, pressure vessels and buildings. This not only poses a risk to safety but also leads to damages, legal issues, and even customer loss.
QA/QC Documents
QA/QC documents are official papers containing information on the processes, checks, tests, and quality assurance and control results. These documents include quality manuals, inspection and test plans, WPS, PQR, WQR, and NCR. Documentation is critical in that it provides audibility, responsibility, and conformity to the set standards and regulations.
Qualification of WPS and Welders
Welding Procedure Specification (WPS) and welder certification is one of the most important steps of QA/QC in welding. WPS qualification involves checking of the welding procedures to confirm that they produce acceptable welds under certain conditions. Welder qualification confirms that welders are capable of performing welding activities in accordance with the specified WPS. Both qualifications are written and kept to ensure conformity and adherence to the set standards.
Welder Qualification
Welder qualification is the procedure of establishing the competency of welders to perform certain welding processes. This involves performance tests in which welders are required to make acceptable welds under controlled situations. The outcome is recorded in Welder Qualification Records (WQR), which acts as proof of their capability and is essential for meeting the industry's requirements.
WPS Qualification
WPS qualification is the procedure of establishing and verifying the welding procedures for compliance with the standard specifications of quality and performance. This involves preparing a comprehensive WPS document that outlines the welding procedures, methods and materials to be employed. The procedure is then validated and the outcome recorded in a Procedure Qualification Record (PQR) to show that the procedure can deliver acceptable and reproducible welds.
QC Prior to Welding
QC before welding is a set of activities that must be completed before actual welding can take place without complications. This involves confirming the quality and dimensions of the materials to be welded, inspecting the equipment to be used in welding, assessing the WPS, and confirming the competency of welders. Further, the fit-up and alignment of the joints are checked to confirm that they are within the standard tolerances.
QC During Welding
QC during welding is the ongoing checking and evaluation of the welding process to ensure that it conforms to the WPS and quality specifications. This involves checking that factors such as voltage, current, and the speed at which the welder travels across the joint are within acceptable ranges. They also look at the technique, interpass cleaning, and weld bead profile as per the set standards. This real time monitoring assists in preventing problems from reaching the defect level.
QC After Welding
QC after welding is a process in which the welds that have been completed are checked and tested to see if they meet the set quality standards. These are simple visual inspections to look for surface imperfections, dimensional control to verify weld dimensions and position, and radiographic, ultrasonic, and magnetic particle examinations. Other methods that may be used to assess the mechanical properties of the welds include destructive testing (DT) methods.
Destructive Testing (DT)
The techniques of DT are characterized by the physical destruction of welded specimens in order to assess their mechanical characteristics and quality. Some of the widely used DT techniques are tensile test, bend test, impact test and hardness test. These tests offer useful data regarding the strength, ductility and toughness of the welds so that they can perform the intended service conditions.
Non-Destructive Testing (NDT)
NDT techniques are employed to assess the condition of welds without compromising them in any way. Some of the methods are the radiographic testing (RT), ultrasonic testing (UT), magnetic particle testing (MPT), liquid penetrant testing (LPT). By using NDT techniques, one is able to identify internal and surface defects such as cracks, porosity and inclusions to ensure the structures welded are safe and reliable.
CERTIFICATIONS

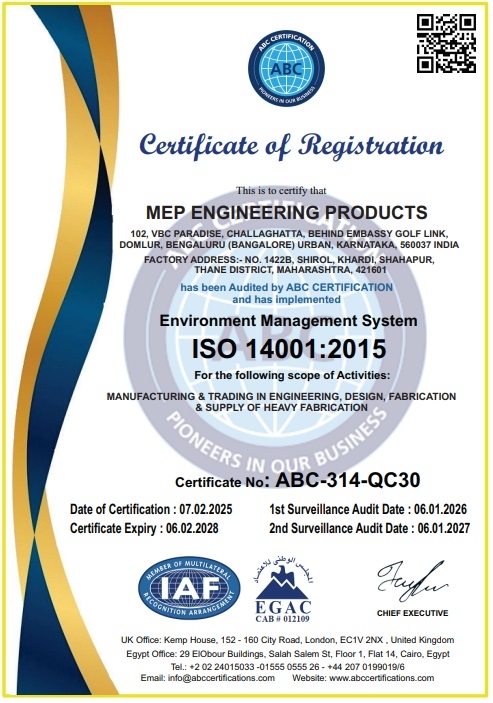

Quality Planning
Define the welding standards (e.g., AWS, ISO, ASME) that need to be met.

Inspection and Testing
Checking for surface defects like cracks, porosity, and incomplete fusion.

Process Control
Ensuring the right materials (e.g., base metals, filler metals) are used and properly stored.

Compliance and Safety
Adhering to local, national, and international regulations and standards.